Quick Changeover Could Make You Win!
- Techam Solutions
- Aug 6, 2022
- 2 min read
Updated: Oct 26, 2022
SMED: A Lean Tool Focused on Reducing Changeover Time

For many people, changing a single tire can easily take 15 minutes while it takes less than 15 seconds for a NASCAR pit crew. That's a huge difference! The time reduction for this changeover time is more than 98%!! The concepts for achieving such unimaginable performance improvement can be applied to any changeover process. In manufacturing, sometimes we forget how much potential is in giving attention to changeover time as opposed to producing faster.
What's SMED?
SMED (Single-Minute Exchange of Dies) is a lean system for dramatically reducing the time it takes to complete equipment changeovers. The essence of the SMED system is to convert as many changeover steps as possible to “external” (performed while the equipment is running), and to simplify and streamline the internal elements. The name Single-Minute Exchange of Die comes from the goal of reducing changeover times to the “single” digits (i.e., less than 10 minutes).
SMED is a lean system for dramatically reducing the time it takes to complete equipment changeovers.
How it works?
In SMED, changeovers are made up of steps that are termed “elements”. The SMED process focuses on making as many elements as possible external and simplifying and streamlining all elements.
Identify changeover internal and external elements
Separate external elements that can be performed with little or no change while the equipment is running
Convert internal elements to external
Streamline remaining elements
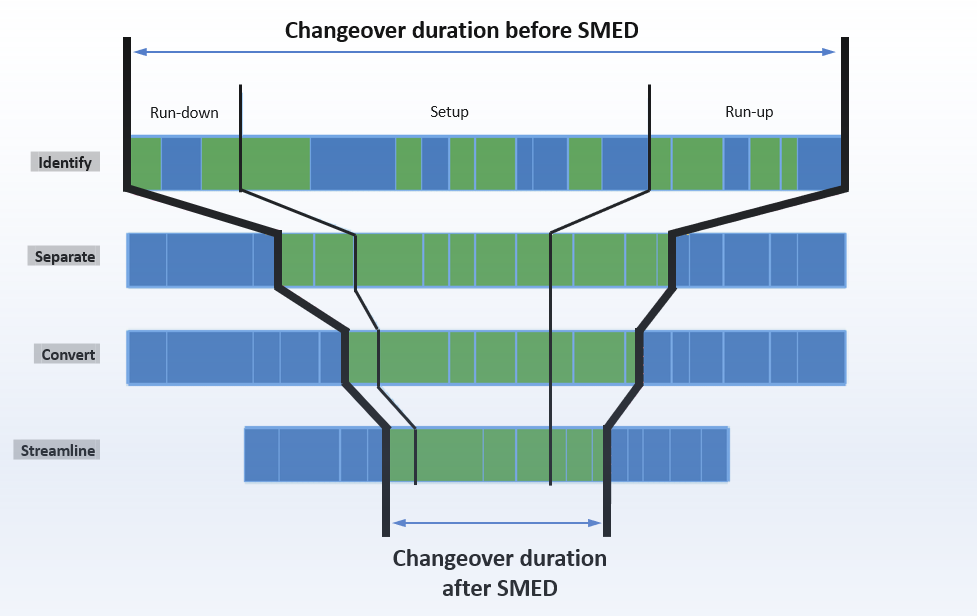
The Benefits
The benefits of SMED touch on major cost, delivery and safety elements of the operations. Some of these benefits are listed below.
Safer environment: More robust changeover process reduces the risk of the safety incidents
Lower Manufacturing Cost: faster changeovers mean less equipment downtime
Smaller Lot Sizes: faster changeovers enable more frequent product changes
Improved Responsiveness to Customer Demand: smaller lot sizes enable more flexible scheduling
Lower Inventory Levels: smaller lot sizes result in lower inventory levels
Smoother Startups: standardized changeover processes improve consistency and quality
Case Study 1: CNC Milling Process

CNC milling machines are considered universal machine tools, capable of producing many different components. There are many techniques available to increase the productivity of the cutting process. Optimizing the cutting parameters, improving the tool path, optimizing the coolant, lubricant, and tool types are just to name a few. However, productivity of machine tools is typically more affected by how long it takes to setup to begin producing the next part. Focused SMED projects result in higher productivity of the machine tool and reduce quality escapes, resulting in significantly higher overall equipment effectiveness (OEE).

Case Study 2: Wire Harness Assembly Process
Wire harness assembly is typically a manual process that require operators to follow the manufacturing steps mapped out on the wire assembly boards. A medium to large wire harness needs one or two plywood as a build board. Depending on the variation of different builds, manufacturers need to switch boards on a regular basis. Reducing the changeover time could result in significantly higher productivity of the harness assembly process. It also reduces quality escapes and improves production throughput while reduces the real estate it demands, making in a smaller production area.