Lean Inventory Management Tools
- Techam Solutions
- Oct 9, 2022
- 4 min read
Updated: Oct 12, 2022
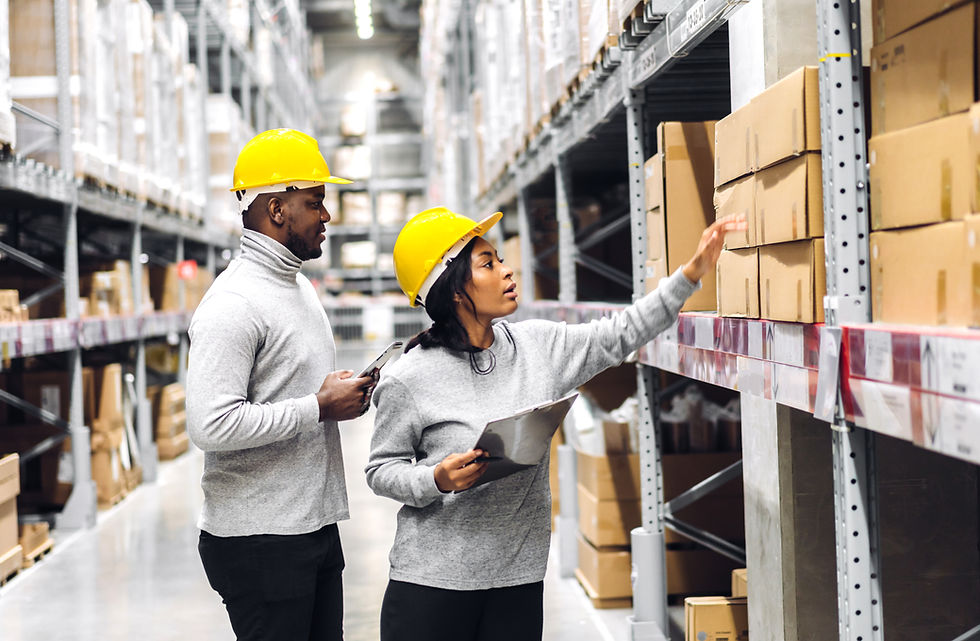
Today’s economic landscape has made Supply Chain issues a common headline. Events like the recent COVID-19 pandemic has shown us the importance of having an effective supply chain even more. For instance, there were months that hospitals and businesses around the world ran out of PPEs and other vital supplies to save people’s lives and keep the business running. How an organization collects inventory data can have a major impact on how quickly they are able to respond to volatile market conditions. Companies can improve their inventory management system by adopting lean practices which increases visibility, provide real-time data, adopting forecasting tools, and better communication with suppliers.
A lean inventory management system emphasizes on keeping only the optimum amount of inventory on hand, while it still ensures that production can meet customer demand. This is most difficult when there are sudden surges in demand, typically resulting in a tendency to hoard inventory. This approach often leads to more problems than it solves. Large volumes of inventory are difficult to manage for companies that are not prepared with systems in place for tracking them. This can lead to many problems such as losing inventory, damaging goods due to irregular storage conditions, wasted time looking for lost inventory, and warranty claims even further down the road.
A lean inventory management system emphasizes on keeping only the optimum amount of inventory on hand, while it still ensures that production can meet customer demand.
Kanban
Many are familiar with Kanban system for production, but the concept can also be applied to purchasing goods from vendors. Kanban systems create additional visibility for organizations including internal and external customers. Kanban’s target is to limit the buildup of excess inventory at any point in a system. Organization can optimize the number of items waiting at supply points and then reduce levels as inefficiencies are identified and improved. When inventory limits are exceeded, an opportunity for improvement is presented.
Visual Management
Successful Lean initiatives rely on Visual Management. Visual Management organizes work and information into an intuitive and easy to see model for what needs to be done, who is responsible, and if it is completed. These practices are commonly used in production and manufacturing environments but they can also be applied to other parts of the organization. In warehouses, Visual Management include graphical cues to organize and manage spaces. Some examples include color-coded labels and signage to identify what and where activities need to be done. These practices also improve communication and collaboration. These will lead to more opportunities for improvement since employees have a clear and concise way to convey information.
Cycle Counting
Cycle counting offers significant advantages over annual physical inventory counts. Only a small percentage of inventory is being counted allowing the business to operate with less disruption. Cycle Counting is more easily managed due to its continual nature and smaller scope than annual physical inventory counts. Due to its continuous natures, cycle counts identify problems in inventory more rapidly than full physical inventory counts. In today’s era of data and analytics, organizations can continuously track the accuracy of its inventory counts and refine counting methods.
Supplier Quality Management
Supplier Quality Management practices can help an organization's supply chain become more lean by reducing the amount of waste created during the manufacturing process. SQM program is an investment on organizations' vendors. Through improvement of the vendors practices the organization can have less to worry about. These support programs ensure that vendors provide materials and components that meet product specifications while decreasing lead time. This not only increases an organizations agility but also reduces the likelihood of manufacturing defects and the need for rework or scrap. Supplier Quality Management practices can help shorten the lead time for products by ensuring that suppliers are able to meet the delivery schedules. This can help reduce the amount of inventory that is held by the organization, which can lead to significant cost savings.
Vendor Managed Inventory
Another way to reduce the burden of inventory management is to move to VMI, Vendor Managed Inventory, for some of the components. VMI shifts the responsibility of the inventory to the supplier. VMI systems rely on the pull principle from vendors. As inventory is consumed the vendor tracks and replaces product as needed.
Lean inventory management tools help businesses reduce cost, improve supply chain visibility, shorten lead time, and improve cash flow.
Conclusion
Lean inventory management is a beneficial approach for businesses especially in times of economic recession. Firstly, it reduces the cost of holding excess stock, as businesses will only hold the minimum level of stock required to meet customer demand. Secondly, it improves visibility throughout the supply chain allowing better understanding of what stock is available and where it is located, resulting in shorter lead time for orders. Finally, lean inventory management can improve cash flow, as businesses will have less money tied up in stock.
About Techam: Techam Solutions is an operations and engineering consulting firm working with small to medium-sized manufacturers, private equity firms and their portfolio companies across multiple industries. We provide a wide range of operations management and engineering services to drive operational excellence and implement solutions that deliver reduced cost, increased performance, and enhance the company’s bottom line. We aspire to be a trusted advisor and a reliable partner who brings meaningful and sustainable value to our clients. For more information, call 316.768.1856 or email info@techamsolutions.com.