Better Decisions with Capacity Analysis
- Techam Solutions
- Jun 7, 2022
- 3 min read
Updated: Jun 16, 2022
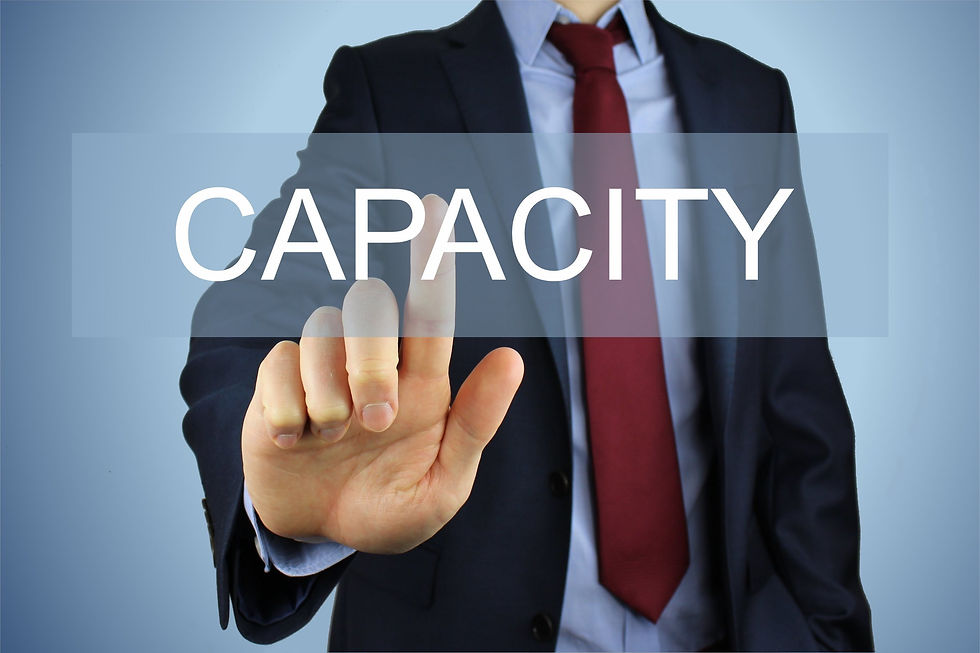
Work It, Make It, Do It, Harder, Better, Faster, Stronger *
The continuous push to do better, seems to have moved to the forefront of many company’s strategies. Work harder. Be more efficient. Make more. The drive to do more, with less resources, is a very real pressure for many companies. A lot of time can be wasted on trying something, finding out it doesn’t work, then trying something else, and seeing only a small improvement. How much more is reasonable to expect? Enter capacity analysis.
How much more is reasonable to expect?
When to use Capacity Analysis
Capacity analysis should be used when we want to determine, what can we do, given the resources that are currently available. It isn’t the right tool for every problem. While the analysis may not present a perfect solution, it can at least show us where to focus our attention and give us a reasonable idea of what is currently possible.
As with any analysis, we need data. This data may not exist, or it may have already been defined and gathered, but not well analyzed, or even analyzed at all. Without data, all we can do is guess and hope.
Capacity analysis is used to determine what we can do given the resources that are currently available.
It’s Time to Get the Data
Let’s consider a company that installs product X onto unit Y, and they want to maximize their throughput in one 8-hour day. At a minimum, we need to know:
The steps or major elements that are involved in this process,
The time needed for each step,
The order in which the steps must be done and if any steps can occur simultaneously,
Any significant limiting factors (e.g., space, personnel, competence, supply chain, etc.)
The data can be collected by conducting a simple time study and creating a process map. For the case of our installers, consider this data table.
Order | Major step or station | Time per step (Min) | People / Station | Sub-steps |
1 | Operation 1 | 87 | 3 | Cut holes, run hoses, build components |
2 | Operation 2 | 104 | 2 | Run connective hoses and wiring |
2 | Operation 3 | 86 | 2 | Run connective hoses and wiring |
3 | Operation 4 | 96 | 2 | No sub-steps |
3 | Operation 5 | 105 | 1 | Build circuit board, attach wiring |
4 | Operation 6 | 107 | 1 | Function check, cleanup, paperwork |

Mr. Data. Analysis Please.
From the data provided, we can see that the bottleneck is the 107-minute step of operation 6. That tells us that we can expect to complete installation on just under 4.5 unit Y’s (480 minutes available /107 minutes at our bottleneck) per day. If our bottleneck were at 96 minutes, we could complete 5 unit Y’s (480/96) per day.
To get to 5 unit Y’s per day, we’ll need to focus on the top 3 bottlenecks. There is no point in trying to make operations 1 or 3 more efficient right now, because they are not the source of the bottleneck. We need to reduce the time spent operations 6, 5, and 2. This could possibly be done by moving some steps around, or reducing the time needed for some sub-steps, or changing the current station layout, or some combination of these actions. This, of course, would result in a larger, more detailed table of steps. We would need times for each sub-step, and to make sure that each sub-step has an updated order. Also, note that the company is using 11 people, at 1045 minutes of labor to complete one installation. This may not be the most efficient solution because we’re only using 4702.5 minutes (1045 minutes x 4.5 unit Y’s per day) for installation but paying for 5280 minutes (11 people x 480 minutes per person) of work.
At this point, it’s time to talk to the company’s management and determine how they’d like to proceed. If they were happy with completing 4.5 unit Y’s per day, I doubt they would have contacted us in the first place. Completing 5 unit Y’s per day is a reasonable goal, that may be achievable with more detailed analysis. However, 6 or more unit Y’s per day is probably not feasible without significant capital investment. The decision about what comes next, or where we go from here is in their hands, but now they can make an informed decision.
Capacity Analysis allows management to make educated decision about defining improvement projects for bottlenecks, balancing the line, or planning for capital investment if a significant increase of the throughput is desired.
* "Work it, make it, do it" from Daft Punk's, Harder, Better, Faster, Stronger copyright 2001.